Additive Manufacturing In The Aerospace Industry
- Muhammad Ahnuf
- Jan 24, 2021
- 3 min read
This blog discusses about the revolutionary Additive Manufacturing method used in the aerospace industry.

Shedding Light On Additive Manufacturing
Today’s products are defined by their ability to uphold both function and form, as present engineering designs are becoming increasingly intricate. Companies have introduced more moving parts in a component with complex geometries. These changes have prompted responses from the manufacturing realm. The breakthrough technology unveiled is Additive Manufacturing which has the ability to revolutionize the manufacturing industry.
Additive Manufacturing (AM) is also known as Three-Dimensional Printing (3D Printing). This approach has transformed the way parts and systems are designed in the aerospace industry. AM method has enabled the creation of lighter and more stronger engineering components.
The AM method uses computer-aided design (CAD) software’s such as Catia, Dassault system or 3D object scanners to direct hardware to deposit material, layer by layer, in exact geometric shapes.
Additive Manufacturing vs Conventional Manufacturing
The primary difference between additive manufacturing is that no tooling is required and it adds material to create an object. On the contrary, when a component is created using traditional manufacturing approach, it is often required to remove material through machining, milling, carving or by other means.

Impact of Additive Manufacturing
AM has overtaken conventional manufacturing methods due to its widely known benefits such as lower costs and swift manufacturing speed. The aerospace and many other industries have reaped both these benefits when applying additive manufacturing to their product development cycles.
The rapid prototyping and production flexibility of 3D printing benefits several applications, as a single 3D printer has the ability to generate limitless breadth of designs respective to its internal dimensions. The key advantage of AM method is that engineers can conceptualize specific designs using CAD software’s and ultimately create multi-dimensional, complex parts at a swift rate.

AM Technologies
Sintering – A process of creating a solid mass by applying heat and pressure without liquefying it. It is similar to a 2D photocopier.
Direct Metal Laser Sintering (DMLS) – A laser is used to sinter each layer of metal powder so that the metal particles attach with each other. DMLS process produces high resolution objects with required mechanical and surface properties.
Direct Metal Laser Melting & Electron Beam Melting – In this method materials are completely melted, DMLM uses a laser to melt each layer of metal powder whilst the EBM uses electron beam of high power to melt the metal powder. This method is used for non-porous objects.
Stereolithography (SLA) – It uses photopolymerization approach to print ceramic objects. A Ultra Violet laser is fired into a vat of photopolymer resin.
AM Materials
Additive Manufacturing process can be performed using several materials. These materials are listed below:
Thermoplastics – This is the most widely used and popular class of AM materials. ABS, PLA and PC materials are examples of thermoplastics.
Metals – Several different metals and metal alloys are used in additive manufacturing.
Ceramics – A variety of ceramic types are also used in additive manufacturing. These include zirconia, alumina and tricalcium phosphate.
Biochemicals – This material is mostly used in the healthcare sector.

AM Applications in Aerospace Industry
Aviation giants such as Airbus, Boeing, NASA have invested heavily in additive manufacturing techniques. In 2014, Airbus started using metal additive manufacturing to produce aircraft components. This was the year they made history by flying a 3D printed part on a commercial aircraft for the first time. Since, then several other parts of the aircraft have been designed by 3D printing.
Moreover, Boeing is another major player in using additive manufacturing for its aircraft. They have invested heavily in startups such as Morf3D and worked on various projects which incorporate AM. The largest project in terms of scale was a 12 ft. long single piece tool for the 777X Aircraft in partnership with Thermowood.
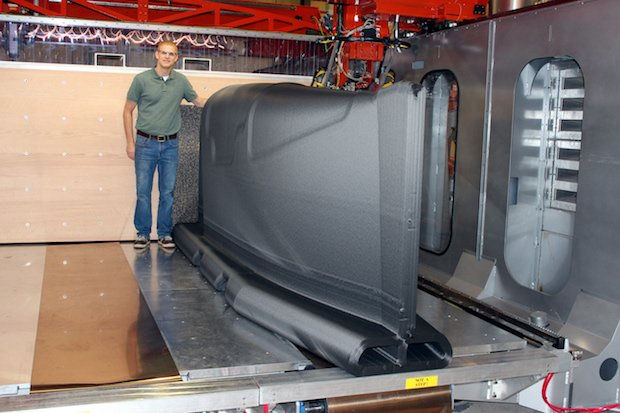
Challenges of AM in Aviation
Size Limitations – The present inability to produce large and odd-sized parts is a major challenge of AM within the aviation industry. According to Deloitte, AM underperforms when compared to conventional manufacturing during production of some large aircraft parts.
Consistency in Quality – This is another challenge faced by AM, specially during production of fully dense metal parts. This is due to non-uniform strength in the plane of layers.

Limitations in Scalability – Keeping stocks of 3D printed parts can be risky for companies using conventional manufacturing methods. This is due to unforeseen events which can occur by storing such parts for the first time.
Costly Materials and Narrow materials range – At present, AM technology mostly uses a very small group of metal powder and polymers to produce aircraft parts. This challenge has to be overcome for wider application of AM.
Future of AM in Aerospace
The future of Additive manufacturing looks optimistic as significant investments have been set in motion. This signals massive confidence in 3D printed production of aircraft components.
Blog Sources (Autodesk.com, ge.com)
댓글